Kevin bei uns auf der Motek
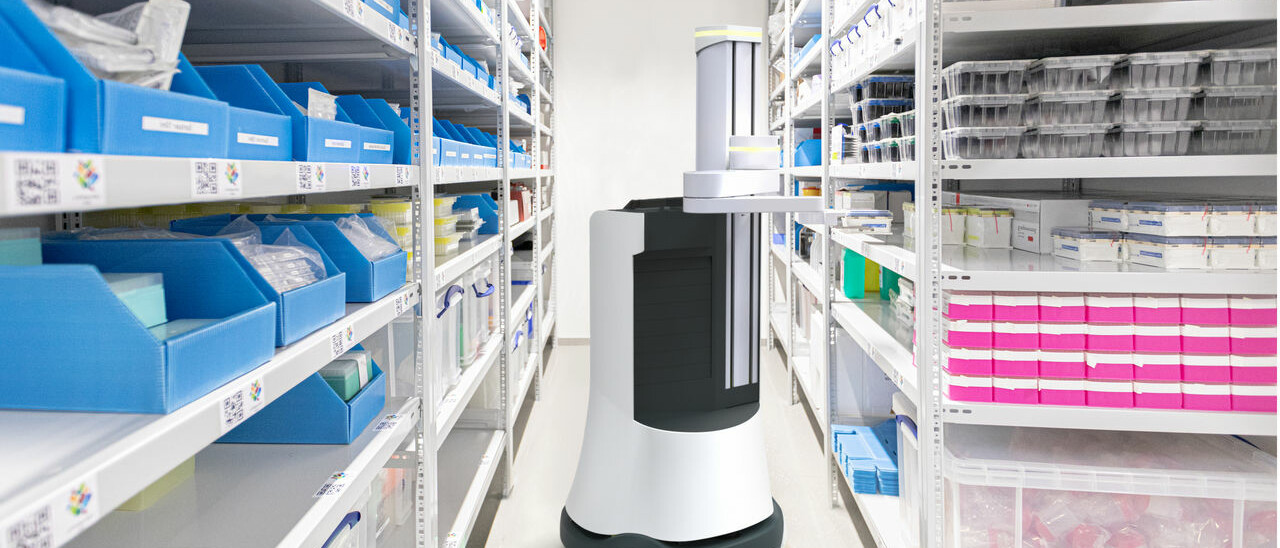
Kevin ist ein Laborassistent, vom Fraunhofer Institut für einfache Tätigkeiten im Labor entwickelt. Die cirp GmbH bringt Kevin mit zur Motek, wo er eine Platte mit mehreren Reagenzien von Gerät zu Gerät transportiert. Die komplette Fertigung und Montage aller Verkleidungsbauteile des ersten Prototyps erfolgte über cirp: Das Gehäuse besteht aus SLA-Bauteilen, die geschliffen, lackiert und montiert wurden. Das ist nur ein Beispiel von vielen Highlights, mit denen cirp nach Stuttgart fährt.
Der 3D-Druck hat bereits etliche Produktionsbereiche erobert. Bitte nennen Sie uns einige Aspekte, die die Vorteile des 3D-Drucks verdeutlichen:
Der 3D-Druck bzw. die Additive Fertigung bringt das Potenzial mit sich, die Entwicklungszeiten durch die Teilefertigung über Nacht deutlich zu verkürzen, die Lagerhaltungskosten durch eine On-Demand-Produktion auf ein Minimum zu reduzieren und Produkte zu ermöglichen, die bisher technisch schlicht weg nicht umsetzbar waren. Die Additive Fertigung, im Speziellen das Lasersinterverfahren, ermöglicht dem Produktdesign durch die absolute Konstruktionsfreiheit nie dagewesene Designelemente, etwa bionische Strukturen, Hinterschneidungen und Überhänge, Leichtbaustrukturen und vieles mehr.
Welche Branchen profitieren besonders von der Technologie des 3D-Drucks?
Im Besonderen profitiert die Automobilbranche nicht nur durch die Kosten- und Zeitreduktion in der Entwicklung, sondern ebenso durch die neu gewonnene Möglichkeit der Mass Customization. Individuell hergestellte Massenprodukte beleben den Automobilmarkt im Interieur-Bereich. Aber auch andere Felder, wie der (Sonder-)Maschinenbau, die Medizintechnik, die Spielwarenindustrie, die Automatisierungs- und Montagetechnik oder auch die Bereiche im Ersatzeilwesen profitieren von den Vorteilen der Additiven Fertigung. Stichpunkte hierzu wären zum Beispiel: Einzelanfertigungen, passgenaue Maßanfertigungen, individuelle Produkte, Herstellung nicht mehr verfügbarer Bauteile mit Hilfe des Reverse Engineerings etc. Diese Aufzählung ließe sich beliebig fortsetzen.
Welche technologischen Hindernisse sind bei der Weiterentwicklung des 3D-Drucks zu überwinden?
Die Additive Fertigung unterliegt seit ihrer Entstehung in den 80er Jahren einem stetigen Wandel. Angefangen hat alles mit der Stereolithographie, woraus sich dann im Laufe der Zeit andere Technologien wie das Selektive Lasersintern, das Polyjet-Verfahren oder das allseits bekannte FDM-Verfahren entwickelt haben. Das Bestreben der Additiven Branche ist dem marktseitigen Druck, Bauteile noch schneller fertigen zu können, gerecht zu werden. Hier stoßen die Entwickler an physikalische Grenzen, die es zu durchbrechen gilt. Auch die Materialauswahl hat sich in der Vergangenheit deutlich erweitert. Der Kundenwunsch, schnell an aussagekräftige, spritzgussähnliche Bauteile zu kommen, wird in der Zukunft kein Wunsch mehr bleiben, dessen bin ich mir sicher.
Welche Zielgruppe sprechen Sie speziell mit Ihrem Unternehmen an?
Ich würde nicht sagen, dass wir mit der cirp GmbH eine genaue Zielgruppe ansprechen wollen. Wir stehen seit nunmehr 27 Jahren für Zuverlässigkeit, Qualität und Kundenservice. Dazu gehören ebenso Großkonzerne wie auch Privatpersonen, die wir mit unserer Expertise im Kunststoffbereich und unserem Netzwerk unterstützen. Unser Ziel ist es, dass unsere Kunden sich bei uns gut aufgehoben fühlen.
Mit welchem Messe-Highlight kommen Sie zur „Sondershow 3D“ während der Motek/Bondexpo 2021 in Stuttgart?
Wir zeigen einen additiv gefertigten Spreizkopf, der mit integriertem Faltenbalg dem Spreizen von Kontaktlinsenblistern dient. Der Übersetzvorgang wird dabei mittels eines Delta-Roboters ausgeführt. Insbesondere das SLS-Material PA2200 ermöglicht hierbei die Herstellung von dünnwandigen Strukturen, die ausreichend elastisch sind, um die Bewegung des Spreizkopfes auszugleichen. Es ist eine Spezialanfertigung.
Außerdem kommt mit: Roboter Kevin. Kevin ist ein Laborassistent für einfache Tätigkeiten und zur Bestückung von Laborgeräten. Unter anderem transportiert der Laborroboter eine Platte mit mehreren Reagenzien von Gerät zu Gerät. Entwickelt wurde Kevin vom Fraunhofer Institut auch für den Dauerbetrieb an Wochenenden, Feiertagen und in der Nacht. Die gesamte Fertigung und Montage aller Verkleidungsbauteile des ersten Prototypes erfolgte über cirp. Das Gehäuse besteht aus SLA-Bauteilen, die geschliffen, lackiert und montiert wurden. Die Bumper im unteren Bereich bestehen aus einem Vakuumabguss in weichem Material.
Und noch ein Highlight aus dem Projekt „Mechanisches Serienbauteil für eine Designleuchte“, das additiv gefertigte Lagerkreuz: „purmundus“ ist eine eingetragene Designmarke von cirp und bietet ein innovatives Portfolio an 3D-gedruckten Tisch- und Stehleuchten. Das Lagerkreuz ist dabei als technisches Herzstück im Sockel der Designleuchte verbaut und dient neben der Befestigung zum Kohlefaserstab und der Platinenhalterung als Druckmechanismus für den An- bzw. Ausschalter.
Ebenfalls im Messegepäck: ein bistabiler Lampenschirm kinetic sls. Die Stehleuchte kinetic sls lädt zur Interaktion ein. Um ihren perforierten Kern schmiegt sich eine zweite, beweglich gelagerte Ebene aus transluzenten Blättern, die die besondere Lichtstruktur aufnehmen. Einfaches Ziehen an zwei gegenüberliegenden Blattspitzen öffnet den Schirm und bahnt dem Licht den Weg für ein futuristisch anmutendes Schattenspiel. Damit vereint kinetic sls facettenreiche Lichtnuancen mit einem innovativen technischen Prinzip.
Und schließlich wird noch eine Industrie-Smartwatch-Schutzhülle gezeigt: Das Start-up-Unternehmen aucobo aus Stuttgart bietet führende menschen-orientierte Smart-Wearable-Lösungen für das industrielle Shopfloor-Management an. Die automatisierte und intelligente Informationsverteilung ermöglicht durch die neue Art der Vernetzung von Mensch und Maschine eine deutlich effektivere Zusammenarbeit und sorgt für eine flächendeckende Digitalisierung in der Produktion und Logistik. Die zusammengefassten Informationen werden per Smartwatch direkt auf das Handgelenk übermittelt. Eine Schutzhülle soll das Endgerät vor Beschädigungen und Schmutz in den Produktionsbereichen zuverlässig schützen. Als Projektpartner unterstützt cirp das Unternehmen bei der Fertigung der Hülle mit ihrem kompletten Leistungspaket von der 3D-Digitalisierung und Konzeption über die Auswahl von Werkstoff und Technik bis zum fertigen Produkt. Der erste Prototyp wurde im 3D-Druck in TPU gefertigt. Das Serienteil wird aktuell mit einem hautverträglichen Material im Spritzgussverfahren hergestellt.