“Sustainability has been on Afag’s mind for a long time”
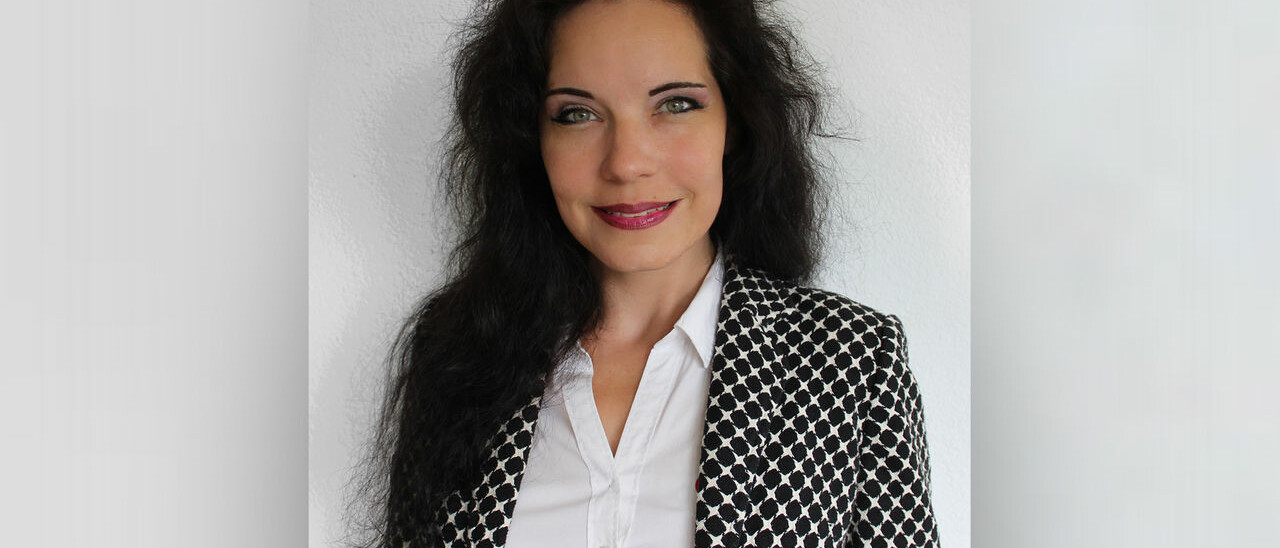
For Anita Renc, Chief Sales Officer of Afag Engineering GmbH, it is important to be live at the Motek/Bondexpo 2021 presence trade fair and to get the important dialog with customers and partners going again. She also talks about trends in assembly and handling technology in an exclusive interview with P. E. Schall. These include mechatronic products with integrated microelectronics or micro-mechanics, as well as embedded electronics that have corresponding software on board.
Ms. Renc, handling systems for assembly and handling technology are Afag’s core business and the heart of traditional industrial production. Give us three keywords that have particularly shaped developments in this area over the past ten years.
- Electric axes with linear motor technology, which allows much higher dynamics and more precise positioning,
- combined turning-gripping modules with the possibility of endless turning (no limitation of the angle of rotation),
- fast transport systems with highest positioning accuracy
… and please three keywords that will change assembly and handling technology in the next ten years.
Smart modules, extracting actionable intelligence from collected data, and balancing innovation with competitive pricing.
Which technological developments are particularly important to be advanced for this purpose? Are there any obstacles or special challenges? If so, which ones?
- Tendency or trend towards mechatronic products with integrated micro-electronics or also micro-mechanics.
- Embedded electronics that have corresponding software such as control algorithms on board and make the products function quasi-autonomously.
- In addition, buses such as OPC UA, OPC UA over TSN, AML, etc., which are based on real-time communication such as Ethernet, are playing an increasingly important role.
- The Iot capability of products will become increasingly important, and the algorithms that generate relevant information for the customer from data should ideally already be integrated into the product.
- In the case of dynamic movements, the topic of functional safety (for example) will become increasingly important; axis controllers must have more and more corresponding capabilities.
- In the future, digital twins will have to be provided for components and subsystems in addition to 3D CAD and CAE data to enable customers to perform virtual commissioning with the appropriate simulation tools.
- The growing dependence on software requires ASAP concepts to ensure the necessary cybersecurity to sustainably protect against corresponding cyberattacks.
With the brilliant development of robotics, assembly and handling technology has taken on a new face. Which development particularly impresses you personally?
The speed at which this technology is adapted to the technical necessities and price possibilities of the applications. The effort required to incorporate these technologies into projects has decreased significantly over the past decade. Programming has become much easier, and companies have rapidly expanded their competencies in this area. Universities offer corresponding courses of study, and the young engineers approach this topic with naturalness and self-assurance. The goal must be that robots or vision systems are no longer programmed by programmers in the future, but configured by the assemblers.
In your view, to what extent has the pandemic situation changed industrial processes and everyday production? Will these be sustainable changes and outlast the crisis?
First and foremost, the pandemic has probably changed the way we work. The possibilities of digital collaboration have existed for a long time, but they would never have gained such widespread acceptance at this speed. I am sure that these insights will persist beyond the crisis and create new opportunities in our everyday work. In addition, however, the crisis has also brought awareness of the value of local supply chains back into focus. Here, with the removal of restrictions, some sourcing will certainly take place overseas again. Nevertheless, I believe that we have become more aware of the risks and that at least a local second source for critical parts will remain strategically in focus.
Which measures or methods do you consider to be particularly effective in moving closer to climate-neutral production?
The topic of sustainability has long been a preoccupation of Afag and is currently being reflected again in a number of projects. Climate neutrality is just one of the important aspects. Thus, not only resource-saving and energy-efficient manufacturing as well as climate-neutral buildings play a role. For example, the service life of the products is also important. For example, we just received a transport system for overhaul from a customer that had been working perfectly for 30 years. It may have cost a few euros more to purchase, but it saves a significant amount of energy for new production and the corresponding expense for disposal over its entire lifetime. And there are many more aspects. I think we have to try to look at this issue holistically.
They know Motek as an outstanding, proven trade fair and as a traditional B-to-B marketplace for assembly and handling technology. How important do you consider a face-to-face event in fall 2021 for both Afag and industry trade visitors?
Motek is not only a traditional trade fair, but also a mirror of current technologies and developments in automation. I think it is important that Afag is represented there because, as an innovative supplier of components and solutions in automation, we can make an important contribution to this. Of course, the uncertainty after the pandemic and the situation at the start of the fair is present in many companies. The performances are therefore perhaps a little smaller than usual for some. But it is important to be there and, also in the sense of Europe as a business location, to get the important dialog with customers and partners going again.